

そして2004年、「この時がいちばん嬉しかった」と三浦が述懐する、“世界最小オン抵抗”が達成された。もちろん当時どこも実現できなかった成果で、三浦は業界の注目を集めた。ここから、量産化に向けての大車輪の奮闘が始まる。心強かったのは、川本や中野たちの参加だ。量産化に向けて強固なチームができあがった。数年の開発期間を経て、三浦と川本は製造部へ異動する。
2009年に研究開発センターから製造部へ移り、国内では初めてとなるSBD(ショットキーバリアダイオード)の量産開始を達成した川本典明が、ロームの組織理念を説明する。
「ロームの場合、研究開発から量産化へは、人ごと移管される、というイメージです。我が子のように愛おしい製品の行方を最後まで見届けたいのが、研究者共通の思いですから」
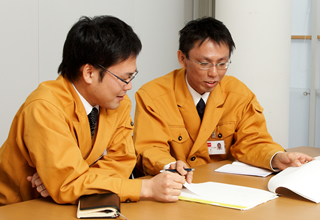
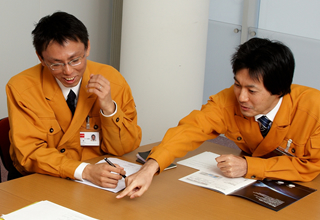
川本の任務は、開発された新デバイスを製造部へ移管し量産ラインを立ち上げること。だが高温プロセスが必要で加工の難しいSiC、従来存在しなかった特有の装置も多く存在し、プロセス数は数百工程に及ぶと予想された。億単位の投資だ。
一方では、市場が立ち上がり始めている時期にさしかかり、競合他社に先行すべく「早くリリースする」ことが迫られている。川本のプレッシャーは大きかったが、それはむしろ彼の奮起を刺激した。
「それまでデバイスの特性だけに注目して研究開発していましたが、コスト、量産性、お客様のニーズ、市場、競合など全体を見渡す必要が生まれ、今までと違った視点で自分のデバイスを見直すことになり、かえって新鮮な気持ちになりました」
国内海外数百社へのサンプル出荷を繰り返し、お客様の評価を得ながらの改善を続けている。
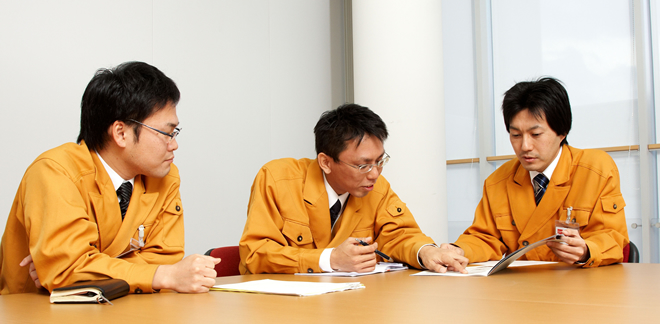

デバイスシミュレーション、デバイス設計、プロセス開発、レイアウト設計、信頼性評価装置、ソフトウェア開発…。こうしたMOS製造プロセスの要素技術の一つひとつを担ったのは、2005年入社の中野佑紀だ。
中野の苦労の一例を上げれば、研究開発用の装置が不安定で、欠陥デバイスが出来ることだった。成膜欠陥、つまり1μmに満たない「破れ穴」が出来たり、たった一個紛れ込んでも許されないパーティクル(微粒子)に悩まされた。原因追究するために顕微鏡に張り付く。デバイスのレイヤー(層)それぞれについて検証しなければならない。
「長い間、『歩留まりゼロ』つまり使える製品が一つも出来なかったこともあります。」さらにSiCウエハはSiの百倍も高価で、試作実験すれば開発コストが桁外れに跳ね上がる。少ないウエハで効率よく開発を進めなければならなかった。先進的なプロジェクトだけに相談相手も少なかった。
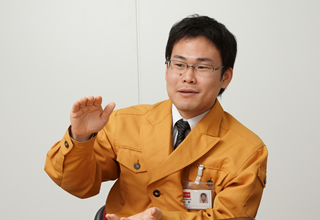
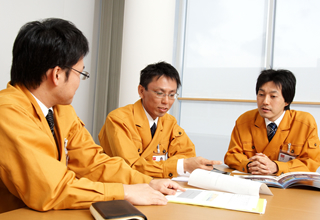
世界一を目指す研究開発だけに常識に囚われない発想が不可欠だが、実際のモノづくりはこうした地道な作業が続いた。中野はこれらの経験を生かし、のちにDMOSFETよりもさらに低オン抵抗なトレンチMOSFETの開発を成功させている。
しかしロームの研究者たちは、象牙の塔に引きこもるタイプではない。彼らは地道な研究の一方、この段階から論文や講演、プレス発表を積極的に行い、「世界初。世界最高性能」「SiCといえばローム」というブランドイメージのアピールに努めることも忘れなかった。
こうしてようやく2007年、製造体制の具体的な準備がスタートした。ロームのバックアップも本格化し、2009年には、ドイツのSiCメーカー「SiCrystal」社を傘下に収め、SiCウエハの安定供給が図られた。