

省電力化のキーデバイスとしてパワー半導体が使われるフィールドは、太陽光発電や電気自動車、産業機器、新エネルギー産業へと広がり、数千億円単位の市場成長が見込まれている。その中でも次世代のパワー半導体として注目されているのが、低オン抵抗で高温環境下での動作特性に優れる、SiC(シリコンカーバイド)だ。ロームは、世界に先駆けてSiCパワーデバイスの量産化を目指し、それを実現した。
SiCパワーデバイスは、小型なうえに電力変換時の損失が少なく数%の省エネが可能で、「日本中のSiデバイスをSiCに置き換えたら原発3台分の省エネを実現できる」とさえ言われ期待が高まっている。
しかし製品化は、容易ではない。原理的には、SiC素子を使えばSiと比べて格段にオン抵抗が少なくなることは周知であったが、製品化するには無数の課題が存在していた。
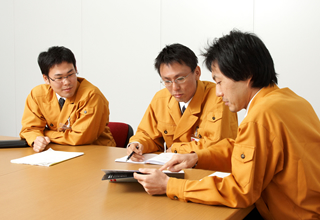
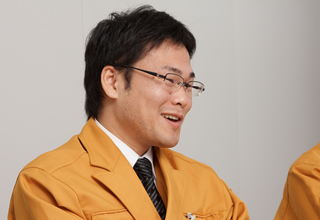
例えばパワーMOSFETの代表的な構造であるDMOS(Double-Diffused MOSFET)構造の場合、基板上に数ミクロンの微細なセルを数万セル配置した構造のため、その製造プロセスは複雑極まりない。今プロジェクトの肝は、まさにそうしたプロセスの一つひとつをSiC用に開拓していくことだった。
2002年、DMOSプロセス研究のスタートと同時にこの任を命じられたのは、三浦峰生だ。この年入社したばかり。「大学でSiCを研究していた」が、当時はロームにとっても数個の開発テーマの一つに過ぎず、孤軍奮闘しなければならなかった。
「SiCそのものは、夢の半導体材料として30年以上研究されています。しかし製品化となるとそのハードルはあまりにも高く、長年研究している競合大手企業もみんな足踏み状態でした。」
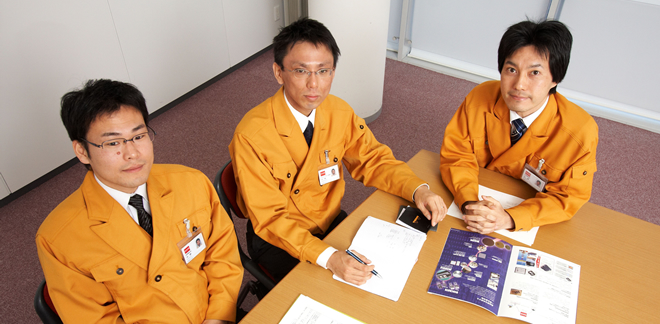

まず先行する論文からヒントを得ることから始めた。しかし、ロームの目標であり半導体企業としてのこだわりは、「世界最高レベルの特性・品質で、かつ、どこよりも早い量産化」だ。
これを実現するには既存の「Siウエハ加工の常識や、他社研究機関のSiCウエハの加工の常識」に依拠した方法論を追随していてはヘゲモニーを取れない。当時はSiC素子を使った試作品はまだ変換ロスが大きく、Siと同程度のオン抵抗値しか実現できていなかった。ロームは、独自の設計思想で開発に取り組まなければならない。
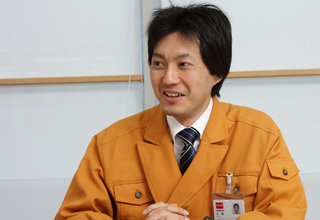
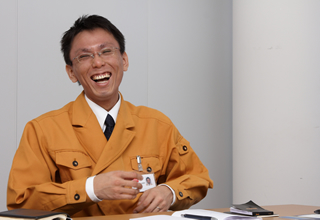
まず基礎的プロセスを確立しなければならない。クリアすべき課題は山積だ。当初は未だ存在しなかった装置も多く、三浦は実験装置を求めて日本中の研究機関に赴き、試作を繰り返すことになる。
「工程ごとに装置を想定し、それを備えておられる研究機関に出かけ、部分的な実験を繰り返しました。まさに日本中を行脚しましたね。」
並行して、SiCに社運を賭けるロームのバックアップ体制も盛り上がり、数億円を投じた研究用クリーンルームも建設された。こうしてまる2年、部分ごとの実験が行われ、それを集積し、三浦の頭の中でプロセス全体が一つの像を結び始めた。